研磨加工、研磨加工機の基礎から応用までを学ぶ
杉下 寛
この『研磨教室』連載の狙い(5回連載)
昔からある精密加工・磨き加工また研磨加工機はどうやってできたのか?
どう発展してきたのか?
本研磨教室では、超精密研磨加工が現代でも最先端技術の1つとして使われている秘訣を解き明かすことで、これからの超精密研磨加工機・研磨加工学が発展して行く礎(いしずえ)を学ぶ第一歩としたい。
講義内容目次
・第1回 研磨加工の基礎と変遷 ―研磨は神代の昔から―
・第2回 現代研磨加工機と研磨加工(シリコン,SiC,GaNなど)の今
・第3回 現代先端研磨加工と研磨加工機の基礎
・第4回 研磨加工用資材と研磨加工機の進化
・第5回 現代先端研磨加工とこれからの研磨加工機の課題と発展
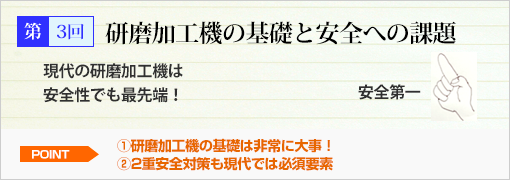
水晶・シリコンウェハはじめ究極の平坦度が必要な各種の超精密部品を研磨加工機で加工している。 研磨加工機には、大きく分けてラップマスター型・オスカー型・ホフマン型の3種類があり、進歩は止まらない。
【1】研磨加工機 進化の歴史と分類
①日本でのラップ盤黎明期
日本製ラップ盤の第1号機は、1953年(昭和28年)に浜井産業が製造した。その後しばらくは2ウェイ機が主流だったが、1976年(昭和51年)に同じく浜井産業によって「油動圧軸受(流体軸受)」の4ウェイ方式ラップ盤が開発された。 図1に、国産最初のラップ盤とそれを改良した技能検定用ラップ盤、ならびに4ウェイラップ盤を示す。
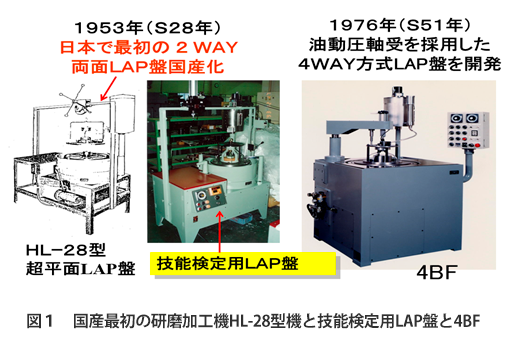
また、図2に、1956年の機械試験所の「審査報告書の結び」を示す。
以上の試験結果で、相互差1μm以下(0.5μm以下も可能)、平行度、平面度とも0.3μm以下とすることが可能であることがわかり、所期の目的が達せられている。ただ、実際の作業にあたり相互差の小さいことを要求するならば、各キャリア間の平均寸法を揃えることが必要で、とくに硬度むらがあるようなときはこの点に一層注意せねばならぬことが以上の実験で明らかになった。
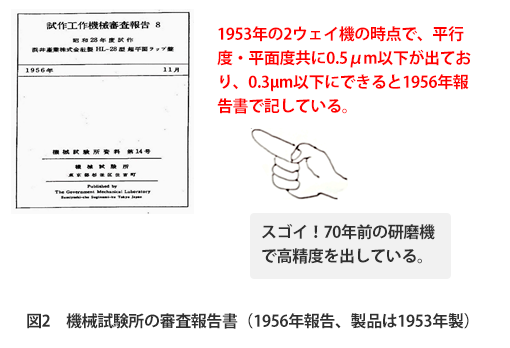
②ラップ盤,ポリッシュ盤の分類
1.単LAP形修正輪式研磨盤(ラップマスター型)
LAP定盤上に数個のリングを置き、その中に加工物を挿入し、加工物に適当な荷重を加えつつ片面を加工する。リング・ワークおよび重しは、定位置で定盤の回転に連れ回りしつつラッピングする。

2.単LAP形搖動式研磨盤(オスカー型)
加工物はあらかじめテンプレートに接着などによって固定し、定盤とテンプレート双方を回転させ、テンプレートは定盤上を搖動運動や円運動をさせてラッピングする。
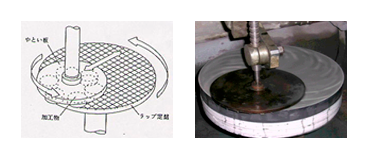
3.遊星運動方式複LAP形研磨盤(ホフマン型)
遊星キャリアに仕込まれた加工物が上下定盤に挟まれ、キャリアの自転・公転により両面ラッピングされる。
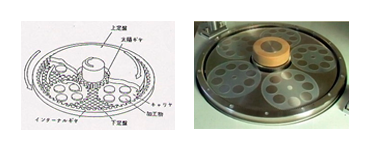
ガラスディスク、ウエハー、石英ガラスの両面研磨で一般的な使用機械
図3に、ホフマン型両面研磨加工機の「ワーク周りの概要」と「ワークの自転・公転方向」などを示す。
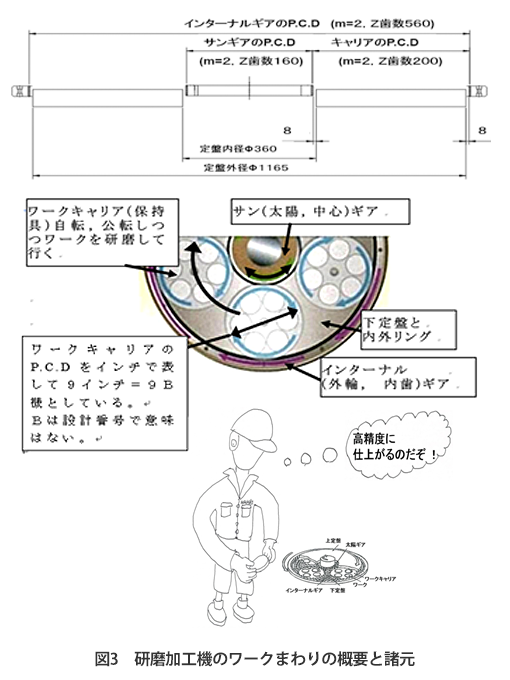
③ワイヤー吊り機の登場
【新たな機構の開発】
ITの進展に伴い必要とされる完成ワークの精度要求は年々高度化し、それに対応する機械精度の向上とともに、新しい機構の開発が進められた。
1.研磨加工機であっても、工作機械と同等の部品精密加工と組付け精度の確保要請。
⇒各部品での精度、公差、組付け時の高精度化が必要であり、同時に組付け時の上下定盤の擦り合わせ精度確保が最重要となる。
2.研磨機独特のユニバーサルジョイント、フラフラ度、定盤の形状、下定盤の軸受等の新機構の開発と改善が求められる。
⇒ワイヤー吊り機構と流体軸受の進化が必要条件。
3.研磨加工時の発熱対策として発熱の抑え構造・逃がし方の方式開発要請。
⇒放熱・冷却システムの開発並びに素材・副資材の適用研究が重要。
4.特にポリシングでは、金属汚染対策・コンタミネーション(ゴミなど)の対策が必要。
⇒フッ素コーティング、完全クリーンルーム対応などが重要。
【ワイヤー吊り機の開発】
両面研磨機のワーク周りのサンギア・インターナルギア・上定盤・下定盤の4軸を全軸回転させる4ウェイ機がこれまでの主流であったが、どうしても 上定盤を吊っているユニバーサル吊りジョイントがもみすり運動をすることから、精度出しに限界があった。そこで、「1本ワイヤー吊りフレキシブルジョイント」が開発され、一段と高精度化が可能となった。今後は、ジョイント部と下定盤を受けている流体軸受部のさらなる進化が展望されている。
図4に、機械構造図を示す。図5に、ワイヤー吊り機のジョイントで使用しているフレキシブルジョイント図を示す。
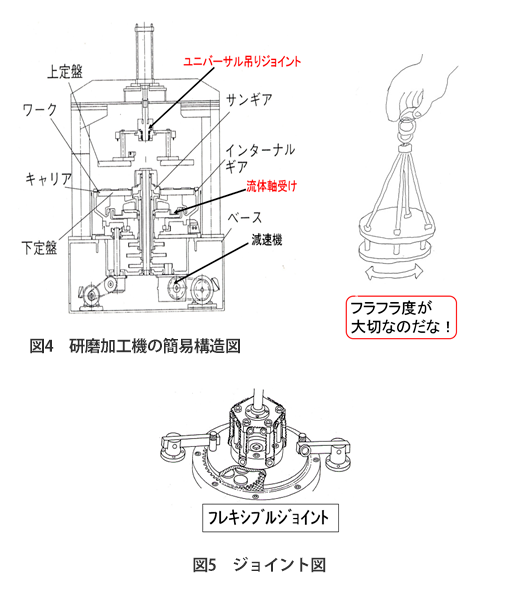
図6にワイヤー吊り部の写真と「3ウェイの平行移動」記事を示す。
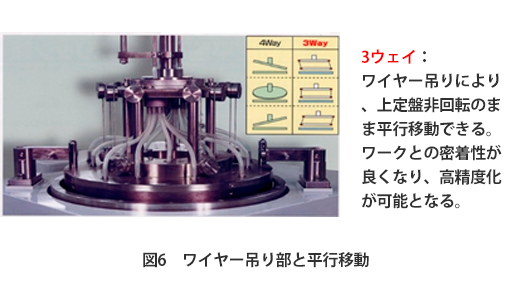
ワイヤー吊りにしたことで確かに精度は向上したが、上定盤が非回転になることで加工能率は4ウェイと同回転なら3割ほど落ちる。従って同能率にするためには、下定盤と公転を約1.3倍にする必要がある。図7に、精度向上を実測した加工データを示す。これはφ200mmのシリコンウエハの加工比較であるが、ほぼ全種類の4ウェイと3ウェイ加工比較で同様の3ウェイ精度良化の結果が出ている。
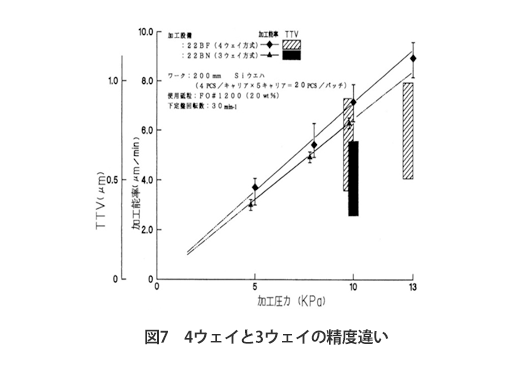
【2】研磨加工機のサイズ選択と安全技術計算
①研磨加工機のサイズ選択
研磨加工機(ラップ盤・ポリッシ盤)の設計は、設計仕様書を書くことから始まる。その前提として顧客ニーズに合致した研磨機の大きさを求めなければならない。研磨機の大きさを確定させるためには、研磨対象となる「ワークサイズ」と効率を考えた「加工枚数」をもとに「ワークキャリアの大きさ」を決めることが第1歩となる。
仮に研磨機が22Bでワークがφ200mmのシリコンウエハとした時、ワークキャリアにΦ200mmの穴が4つ空くことになる。それぞれの穴の間隔(縁から縁までの距離)を15mm以上の適正値にし、オーバーハング量を決めることで4穴の配置が決定される。
こうしてワークキャリアの大きさが決定されることにより、適合する研磨加工機の大きさが確定される。
第8図に、キャリアの設計図例を示す。
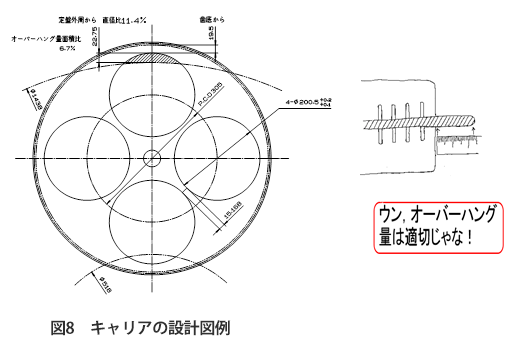
②安全に関する技術的計算
研磨機で特に安全に直結する計算すべき点は、「定盤の重量を支えるメインシリンダーの大きさ計算」はじめ「締結ネジの計算」「締め付けトルク確認計算」、「たわみ計算」など、各種強度計算・安全率計算がある。 設計の仕様書を作る時には当該部分の強度計算をして安全率を確認しておくことが肝要である。
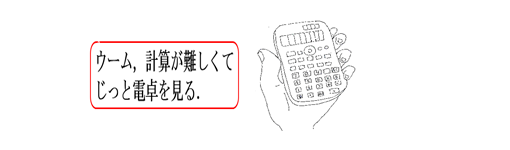
【3】安全装置について
安全装置については、現在、非常に強い要望が出されている。
①安全対策
【大型研磨機 上定盤対策】
日本製の研磨機であっても、安全に対する厳しいユーザーの目が増え、特に大型研磨機では上定盤落下に対する安全性が重要視されるようになってきた。
当社大型機では、上定盤のメインシリンダーネジ部が緩むなどで切断した場合の安全装置として、「落下防止フォーク」を標準仕様としている。
さらに上定盤そのものの落下を防ぐ「第2落下防止用アーム(通称カニはさみ)」の安全仕様もある。図9に、大型研磨機の2重安全装置を示す。
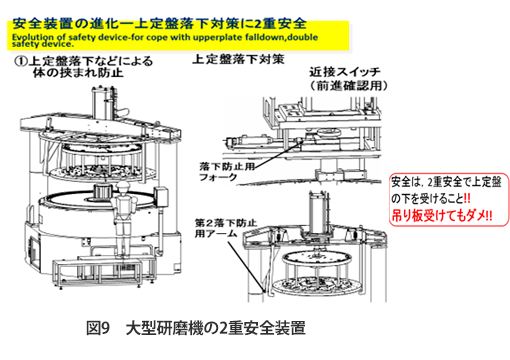
【安全カバーのセーフティロック】
ラップ盤(さらにホブ盤も*)において「可動部分フルカバー」かつ「機械稼働中はドアを開けることができない」仕組みを取り入れ、安全性を高める方法もある。
図10に、ラップ盤9BFへの「セーフティロック」取付け例を示す。
*(ご参考)弊社製品ホブ盤「Nシリーズ」では、正面扉の「セーフティロック」は標準装備となっています。
ラップ盤の安全カバーへのセーフティロック装着例
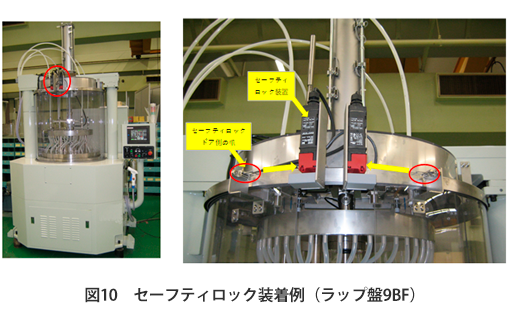
②地震対策
大震災の時に、ユーザー工場に設置されていた32B型機(20数TON)が機械全体で横移動してずれたことがわかった。この状況を踏まえ、大型機といえども地震対応としてベースをアンカー固定する必要があるとの考え方が一般的となった。現在では大型機を設置した工場では、ほとんどが地震対策を施している。
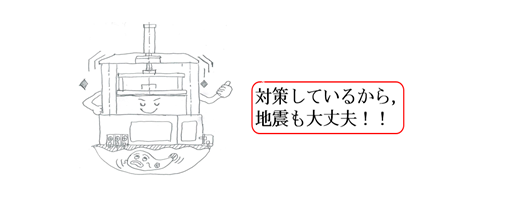
追伸
足利の山火事について
2021年2月~3月にかけて足利工場のある栃木県足利市で大規模な山火事が起き、神社も含めて山1つ全体が焼けるなど大きな被害が出た。工場とは反対側の山であったが、煙が工場まで流れてきて相当に煙たかったことが強烈に記憶に残っている。
山火事がたばこの不始末によって起きたとの見解も出て、約1ヶ月後にやっと一段落した。
その間、たくさんのユーザーから大丈夫か?とのご心配やお気使いのご連絡を戴きましたことに、この紙面を借りて御礼申し上げます。
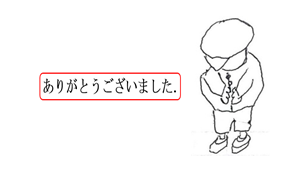
次回第4回では「高精度化への挑戦」として研磨加工機がどのように変わって来たかを、さらに詳細に記していきたい
現場からの一言
一覧へ2020/11/20
現場からの一言
2020/11/20
輸出管理はお任せください
2020/09/25
現場からの一言
2020/09/25
コロナ禍における東京営業部奮闘記
2018/12/11
現場からの一言
2018/12/11
「精密ホブ盤120A」最終号機を出荷!!
2018/10/03
現場からの一言
2018/10/03
“工場今昔風景”そして“今どきの若者は”
2018/07/11
現場からの一言
2018/07/11
「自動化」の先には何が!
2018/01/10
現場からの一言
2018/01/10
精密ホブ盤組立の効率化を目指して
2017/03/03
現場からの一言
2017/03/03
足利工場安全衛生を振り返って
2016/11/11
現場からの一言
2016/11/11
人手不足の中国――自動化機械の時代に
2014/07/01
現場からの一言
2014/07/01
韓国『両頭フライス盤』事情
2014/05/27
現場からの一言
2014/05/27
機械メンテナンスのハマイエンジニアリング
2014/03/18
現場からの一言
2014/03/18
『機械に魂を入れる組立』
2014/02/10
現場からの一言
2014/02/10
シリコンウェーハ 平坦度への挑戦
2014/01/08
現場からの一言
2014/01/08
新登場 浜井のグラインディングマシン
2013/12/04
現場からの一言
2013/12/04
信頼関係に基づいた購買業務
2013/11/01
現場からの一言
2013/11/01
広域マーケットで奮闘中
2013/10/02
現場からの一言
2013/10/02
研削加工の不思議
2013/09/05
現場からの一言
2013/09/05
中国営業はお任せください
2013/08/26
現場からの一言
2013/08/26
設計技術グループに配属となって
2013/07/10
現場からの一言
2013/07/10
浜井のラップ盤
2013/06/11
現場からの一言
2013/06/11
時代と共に進化する機械
2013/05/15
現場からの一言
2013/05/15
システムの進歩
2013/04/30
現場からの一言
2013/04/30
危険予知活動を日常作業にも
2013/04/08
現場からの一言
2013/04/08
Let’s meet the demand of our Customers!
2013/02/12
現場からの一言
2013/02/12
躍動する東京営業部
2013/01/31
現場からの一言
2013/01/31
工作機械の開発設計
2012/12/05
現場からの一言
2012/12/05
浜井産業の歴史を支えて来たもの
2012/10/19
現場からの一言
2012/10/19
ビジネスのフィールドは海外へ
2012/09/19
現場からの一言
2012/09/19
『キサゲ』のお話し
2012/09/03
現場からの一言
2012/09/03
工作機械「生産管理」の習熟と伝承
2012/07/27
現場からの一言
2012/07/27
浜井のホブ盤
2012/07/17
現場からの一言
2012/07/17
お客様のご要望にお応えして